Boosting Efficiency and Reducing Costs with Centralized Feeding Systems in Blow Molding
In the plastic blow molding industry, the centralized feeding system helps reduce costs and improve efficiency in the following ways:
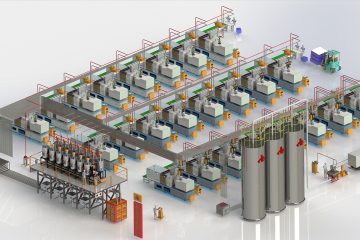
-
Precise Measurement and Ratio Control: The centralized feeding system can accurately control the ratio of different raw materials, reducing errors from manual operations, ensuring accuracy in the material mixing process, and thus reducing waste and rework, while improving raw material usage efficiency.
-
Reduction in Labor Costs: The system reduces the reliance on manual intervention, lowering labor costs. Additionally, operators can focus their attention on other higher-value tasks, increasing overall production efficiency.
-
Improved Production Stability: The centralized feeding system ensures continuous and stable supply of materials, avoiding production interruptions or efficiency losses caused by human errors or material shortages.
-
Reduction of Material Waste: With precise control and monitoring, the system minimizes over-supply or under-supply of materials, thus reducing unnecessary waste and lowering costs.
-
Increased Capacity and Efficiency: The centralized feeding system enables continuous and fast material feeding, shortening production cycles, improving equipment efficiency, and boosting overall production capacity.
-
Real-Time Monitoring and Optimization: Modern centralized feeding systems are typically equipped with real-time monitoring functions, which allow adjustments to the production process based on data feedback, optimizing material usage and further enhancing efficiency and cost reduction.
In summary, the centralized feeding system helps the blow molding industry achieve cost reduction and efficiency improvement by enhancing precision, reducing waste, lowering labor costs, and improving production efficiency.